Innovation teams and plant managers constantly look for new ways to improve productivity through automation. Yet managing large, asset-heavy industrial facilities has proven to be uniquely challenging and labor-intensive. In response to this need, creative solutions have recently emerged. New kinds of autonomous robots are now available that can traverse facilities designed for humans and gather data from complex environments without needing a human operator. These autonomous robots represent the next step in the journey to truly autonomous industry.
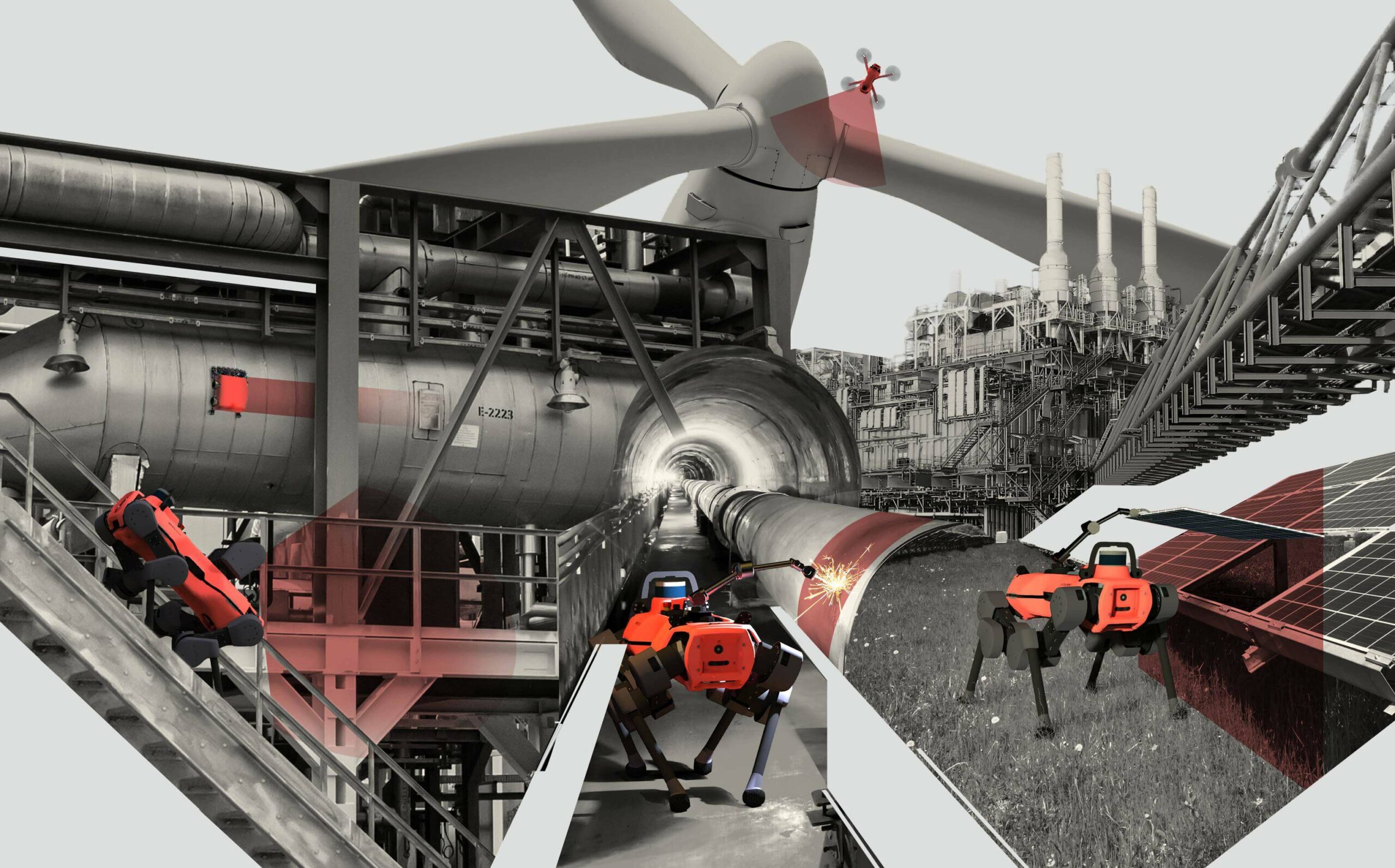
Asset-heavy industries are undergoing a profound transformation in digitalization and automation. Some of the most physically extensive and equipment-dense industrial facilities include power generation and distribution complexes, oil & gas installations, chemical plants, and mining sites. Due to their complexity, these industries require the constant physical presence of on-site personnel to verify correct operation and react to problems through maintenance work.
While human workers are a flexible way to accomplish a wide array of tasks, this human-centric approach has three fundamental issues:
- Lack of available and qualified workers: Industrial operators face an accelerating demographic shift. While older people move into retirement, companies struggle to find young people who can and want to take over the open positions. The European Centre for Vocational Training estimates there will be 1.5 million unfilled plant operator positions by 2030 in the EU alone.
- Limited productivity: Human workers have a limited ability to gather and analyze data, which can lead to unplanned downtime and inefficient use of assets. Computerized solutions can detect and analyze data more accurately, reducing downtime and costs. A study found that undetected equipment issues cause $270 billion in yearly downtime costs for major industrial organizations.
- Work-related accidents: Industrial accidents can have severe consequences for on-site workers and the environment. Not surprisingly, accident reports suggest the vast majority of industrial accidents are caused by human error. And work-related accidents and injuries cost EU €476 billion a year, according to the European Union Information Agency for Occupational Safety and Health (EU-OSHA).
These issues are causing a shift toward a more machine-based approach built on connected equipment, the Industrial Internet of Things (IIoT), and robotics. With the development of fully autonomous and AI-powered robots like ANYmal from ANYbotics, it is now possible to create truly autonomous industries.
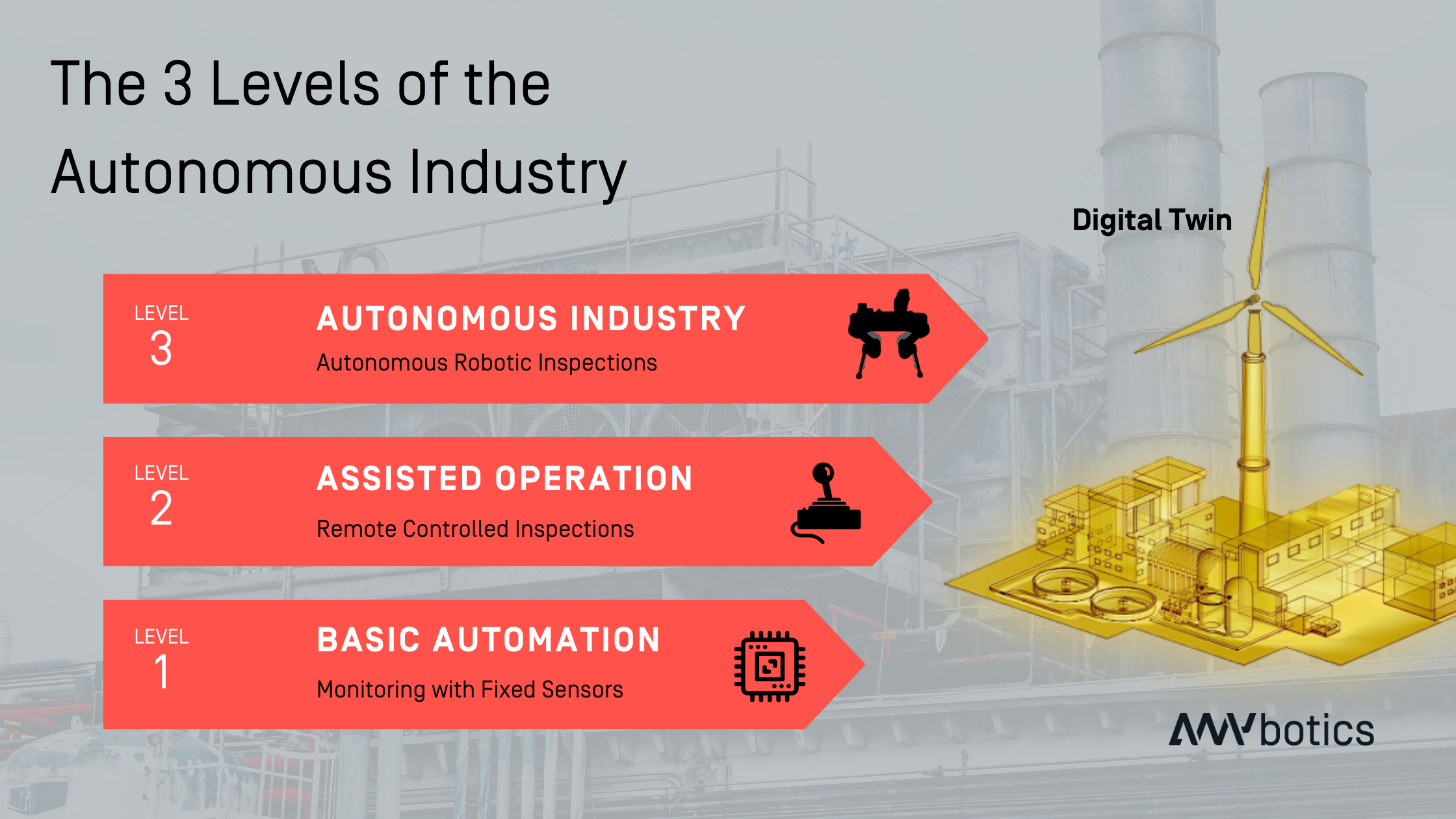
Three levels of machine-supported automation of facility inspection by (1) IIoT sensors, (2) remote-controlled inspection devices, (3) fully autonomous robots.
Autonomous Industry’s Core – The Digital Twin
Crucial to a new level of automation is the digital twin concept. In addition to being a visual, three-dimensional reconstruction, this digital replica incorporates process data, including temperatures, pressures, and flow rates, among many other parameters. With a digital twin, plant operators can collect, visualize, and analyze information from the facility to examine and improve physical processes.
For the digital twin concept to work, it must be intimately connected to the physical site to ensure that reality is correctly represented. The digital twin must be fed with large amounts of reliable and real-time data to accurately represent the state of the physical site. A continuously updated and holistic view is needed to derive actionable insights. Based on this data, the digital twin can prompt operators to take action. The action may involve taking a piece of equipment offline for maintenance, for example, or changing the operating parameters of a production process to improve its output. In general, the digital twin is autonomous industry’s core: determining and instigating relevant actions to supervise, manage, and continuously improve the functioning of the physical infrastructure.
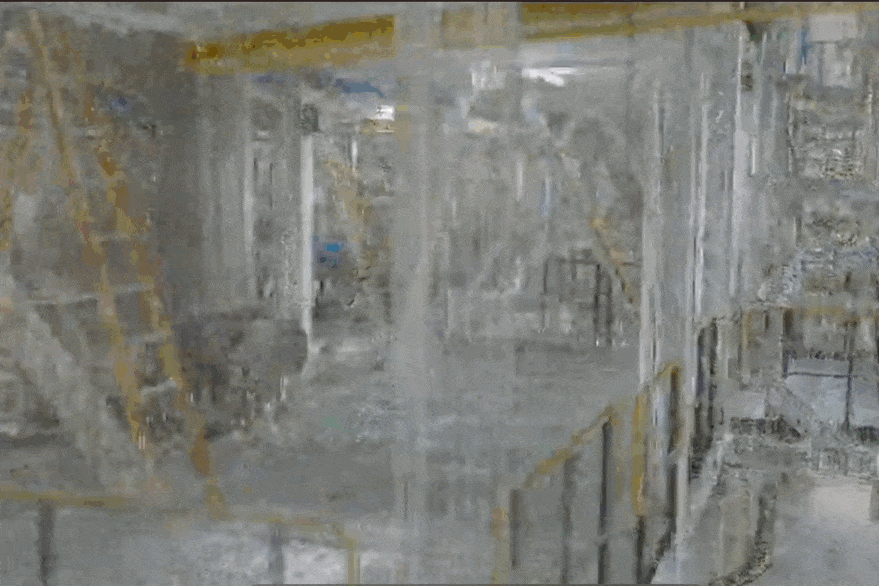
Facility data is fed into and processed in the digital twin. ANYmal creating the 3D scan of a chemical plant.
Level 1 – Basic Automation with Stationary Equipment
Basic automation involves connected equipment with built-in sensors. The Industrial Internet of Things (IIoT) brings many advantages, such as monitoring motorized equipment via vibration and temperature sensors to predict failure before it happens. Embedded transducers enable a much higher frequency of measurement and closed-loop control. For example, if a piece of equipment begins to overheat, it can sound an alarm or automatically shut itself down.
Limitation: A constraint to stationary sensors is that each measurement requires a unique transmitter, meaning that data collection is limited to a particular spot or piece of equipment. Sensors placed in fixed locations can’t detect many problematic conditions. Gas and liquid leaks can occur through almost any flange or seam. Rust can appear in many places. Sensors cannot detect missing parts like screws or nuts. Cracks can form in ways that are difficult for fixed transducers to ascertain. Adding more measurement transmitters to try and identify all these conditions adds cost and complexity to the maintenance effort.
Therefore, stationary sensors provide only a basic level of automation.
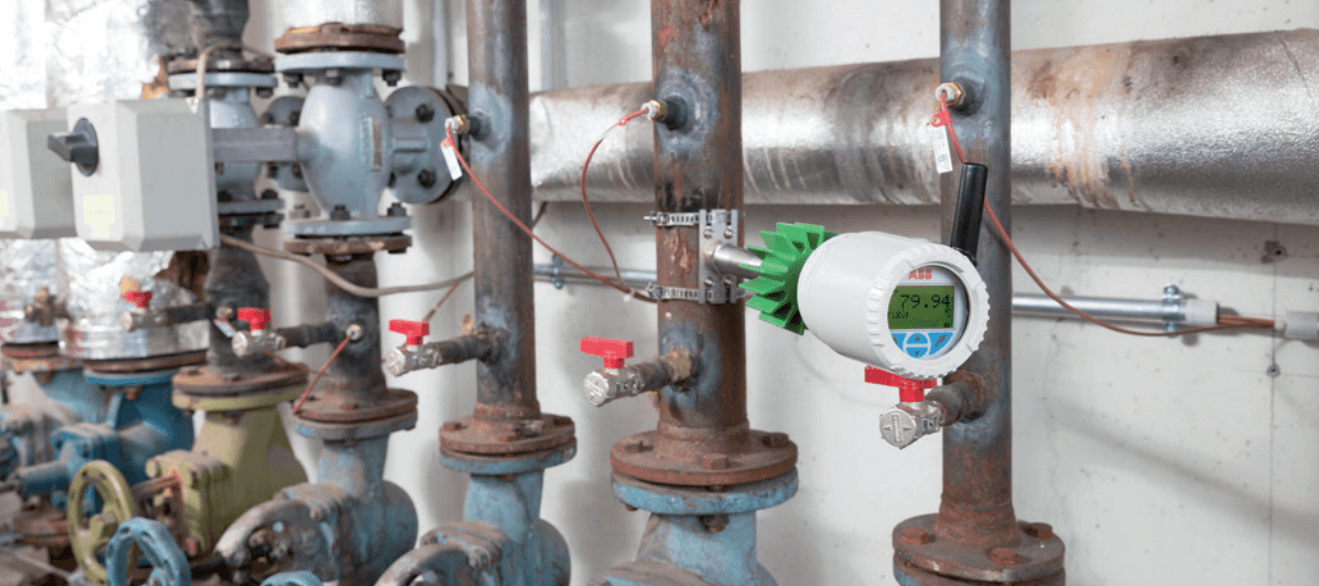
Wireless temperature sensors enable the addition of measuring points throughout operations. Courtesy: ABB
Level 2 – Assisted Operation via Robotic Tools
Robotic tools can help operators to monitor crucial processes in large and hazardous industrial environments. Remotely piloted drones can fly up the side of large tanks, smokestacks, and other tall equipment, capture high-resolution images, and wirelessly transmit the pictures back to the operator in real-time. Remote-controlled crawlers with magnetic wheels can travel up metal surfaces or down pipelines to perform inspections. From a safe distance, human operators can teleoperate these robotic tools and avoid the need to enter confined spaces or raise a scaffolding, saving on time and costs.
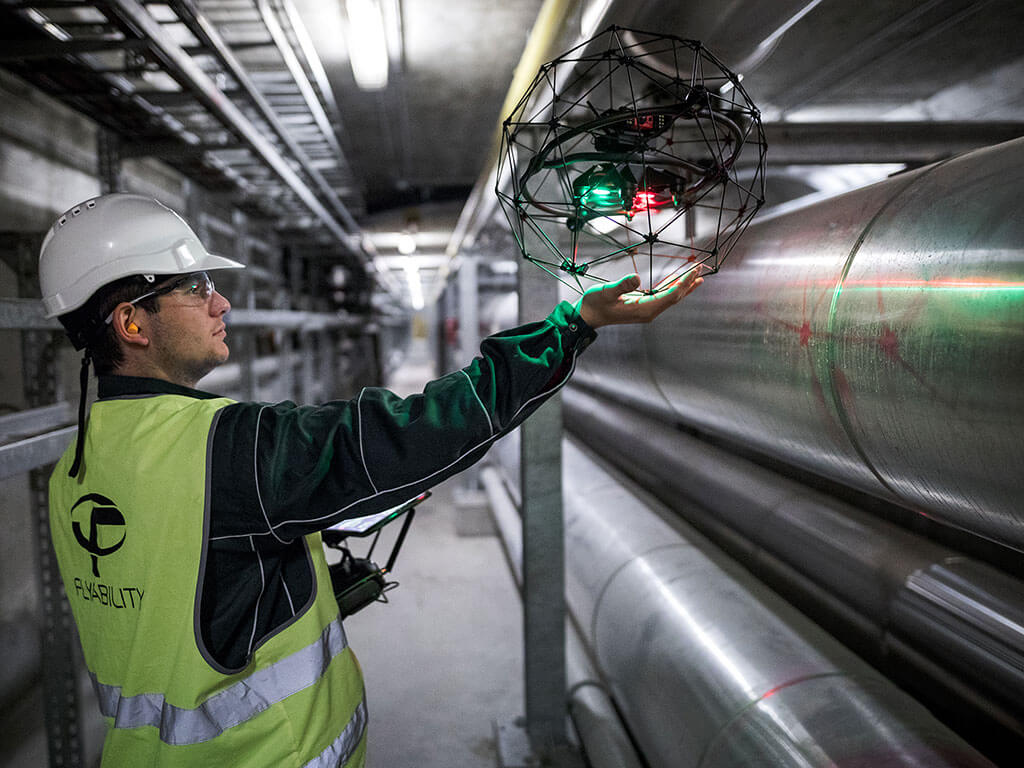
Remote controlled drone inspection in hard to reach locations. Courtesy: Flyability
Limitation: The crucial drawback to this use of robots is that there is a one-to-one relationship between the operator and the robot. And the user of the robotic tool needs at least the same level of expertise as the user of a manual tool. As a result, the same number of on-site personnel is necessary to run the facility.
Level 3 – Autonomous Robots Bring Scalability to Automation
Poised to revolutionize the management of asset-heavy industrial sites, autonomous robots that provide mobile sensing for entire facilities are now available. Advances in artificial intelligence, more powerful computer processors, and miniature sensors enable a new breed of highly mobile and autonomous robots. This novel robot type allows firms to handle a new dimension of measurement complexity and completeness than fixed sensors or remotely controlled robots.
A ground-based robot can carry a reasonably heavy payload of equipment – 15 kg of instrumentation. Consequently, robots like ANYmal can bring a robust set of high-quality, sensitive measurement and recording capabilities wherever it goes. Instead of trying to cover each potential problem with its own measurement transmitter, mobile sensing can bring the transducer to the problem rather than the other way around.
These new robotic devices fundamentally change the picture from a one-person-one-device relationship to a one-person-many-devices hierarchy. As a result, it now becomes possible for one supervisor to monitor and manage a complementing workforce of robots.
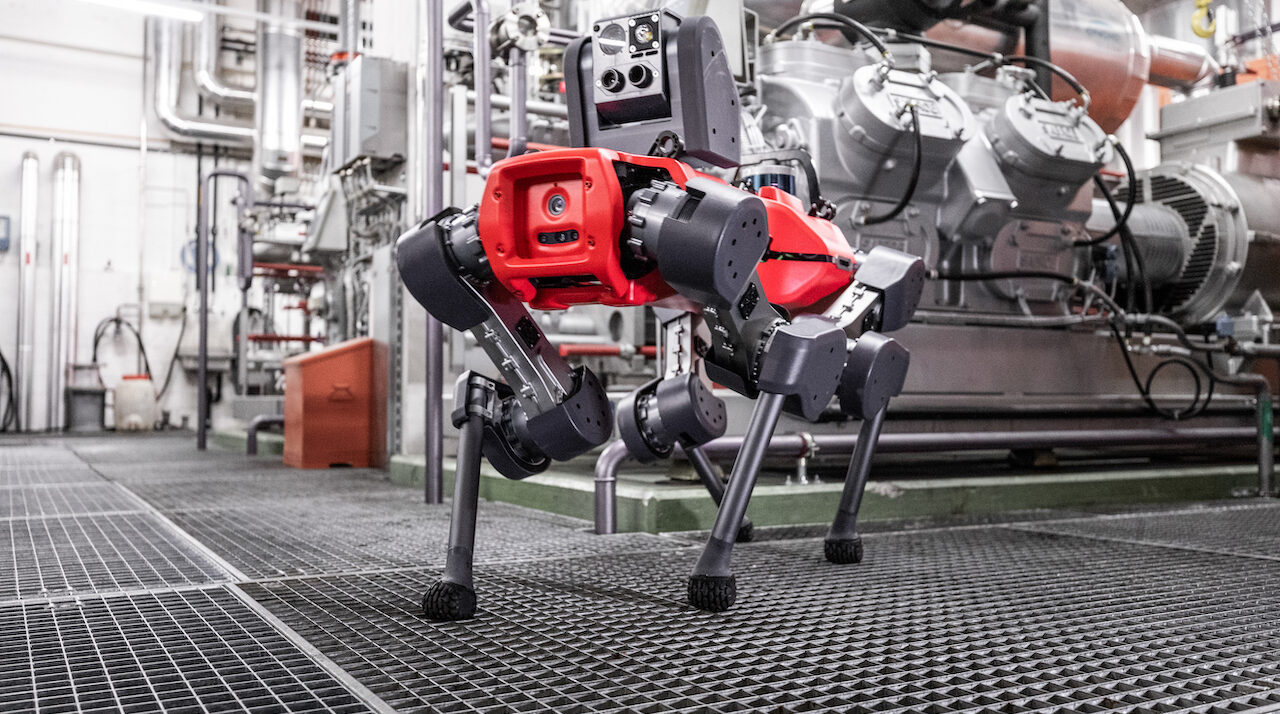
The legged robot ANYmal detects early signs of operating problems by examining equipment health.
Pioneering New Levels of Autonomy
The best-in-class solutions in this category, such as ANYmal from ANYbotics, provide maximal flexibility through high mobility. ANYmal is a four-legged robot that can easily traverse steps and staircases, something difficult or impossible for robots with wheels or tracks to accomplish.
ANYmal’s navigation is unparalleled in narrow spaces, enabling it to avoid obstacles and collisions and plan new routes to its assigned destination. Based on LIDAR and depth camera technology, the robot always knows its exact position indoors and outdoors without needing additional infrastructure such as beacons or visual tags.
Artificial Intelligence brings the inspection capabilities of ANYmal to a new level. ANYmal’s onboard inspection intelligence provides the ability to analyze inspection data on the fly to trigger additional behavior to maximize the quality of the inspection results. For example, ANYmal positions itself differently if an inspection point doesn’t provide the relevant information, such as adjusting the angle of inspection to avoid glare on a gauge and crouching down to take a closer look.
Autonomous mobile robots represent a paradigm shift. They work more accurately, reliably, and safely than a human operator. Because of their exceptional mobility, systems like ANYmal can maneuver through entire sites such that one device – with no additional infrastructure – can fully cover a facility. Four-legged, autonomous robots are redefining the approach to data collection.
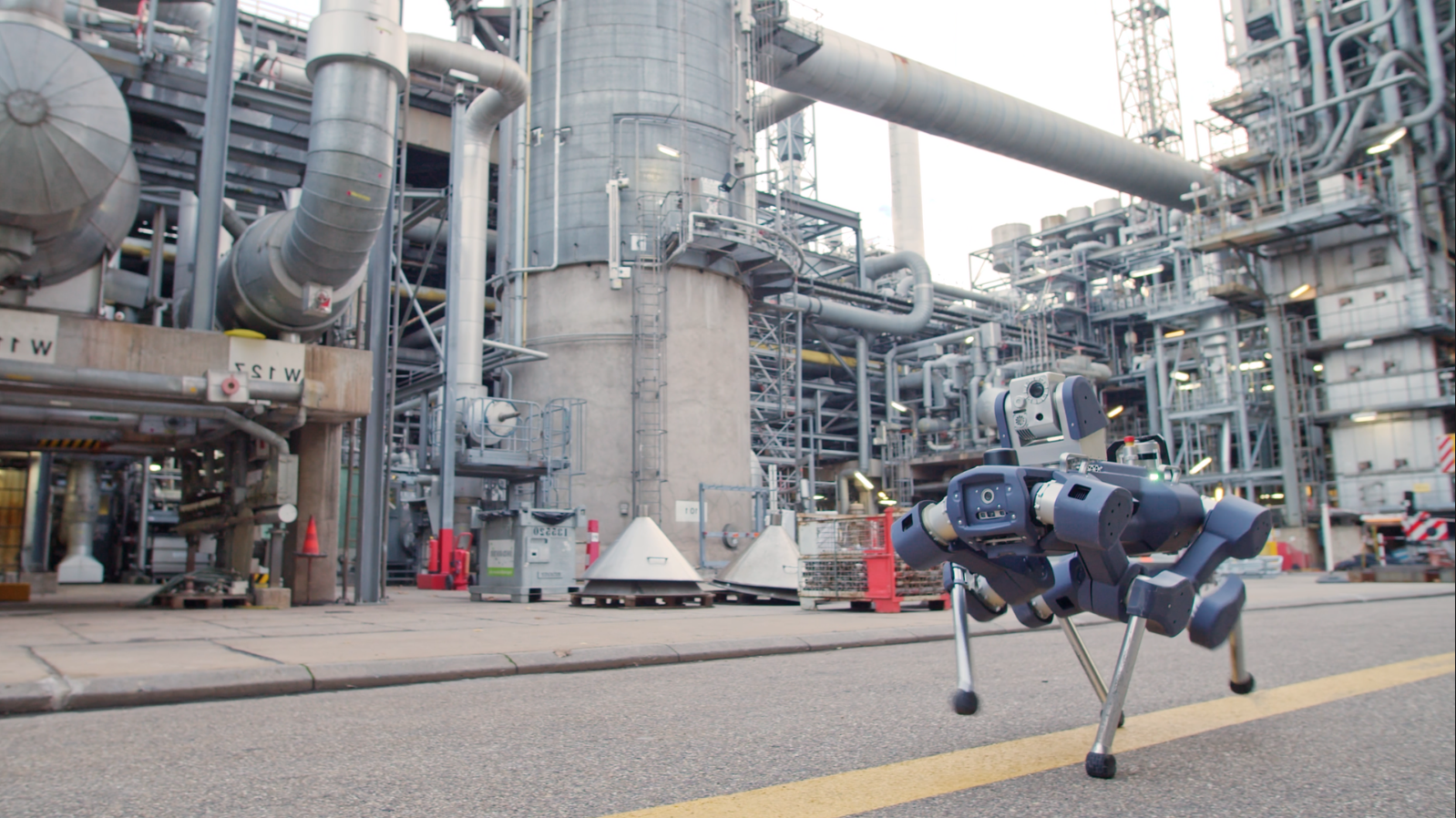
Three Levels of Automation – Each Plays a Role
The three levels of automation outlined here are complementary, and each performs an indispensable role.
Because of the availability of AI-driven and highly mobile machines, companies are integrating autonomous robots to take the next step in digitalization and automation. Due to the flexibility and scalability of autonomous robots such as ANYmal, existing brownfield plants can be easily retrofitted. In the future, new plants are already planned that will be specifically designed for robots. These new facilities will need less overhead required by people in the form of living quarters, HVAC, desalination, and safety requirements.
Autonomous mobile robots elevate and enhance the work environment and the very nature of industrial work. People are kept out of harm’s way, and the work is made more interesting. Robots do the dirty work, and humans obtain more opportunities to employ their creativity and problem-solving capabilities.