Steel manufacturer Outokumpu and ANYbotics partnered to deploy the ANYmal robotic inspection solution at three different sites in Finland, Germany, and Sweden. These robots should improve occupational safety and productivity. How does that work? production.de talked to Outokumpu and ANYbotics on 5 October 2023 to find out.
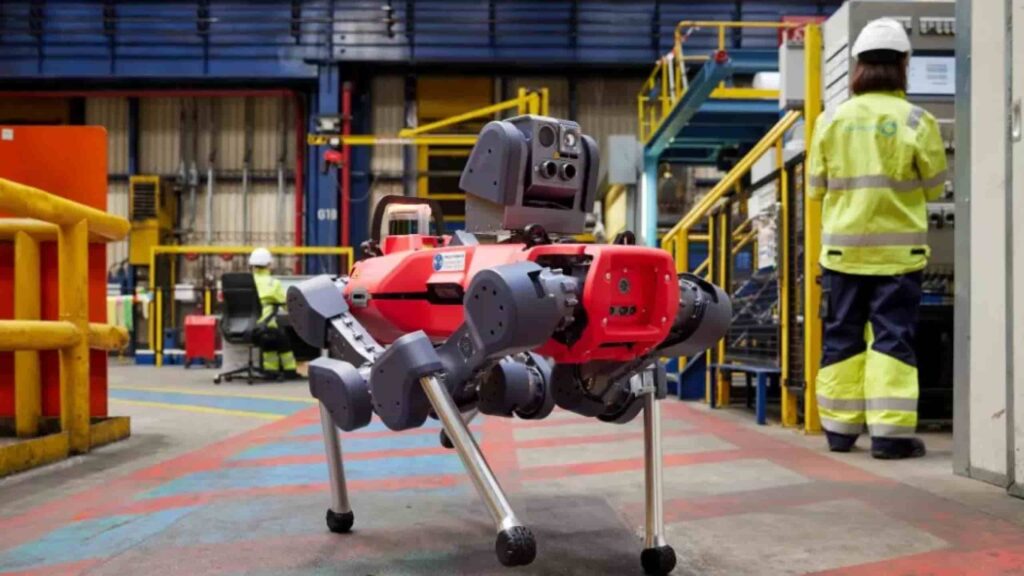
Rosie, the Krefeld running robot, can work for approximately two hours before requiring a two-hour charging period. If the path is blocked, the device will find an alternative route.
(Courtesy: Outokumpu)
The steel manufacturer Outokumpu is conducting several pilot projects to test the automated inspection of machines and systems. As part of this effort, the company has purchased three ANYmals. These four-legged robotic inspectors undergo several weeks of training, similar to new employees before autonomously carry out their inspection tasks.
The first robot arrived in Krefeld in June 2023. The second and third robots, located in Sweden and Finland respectively, were added later to gain initial experience. produktion.de magazine interviewed the following key people about this initiative:
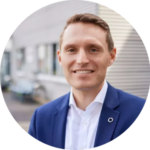
Thorsten Piniek
VP Health and Safety
Outokumpu
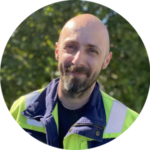
Sebastian Kegel
Occupational safety
Outokumpu
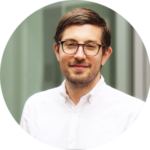
Enzo Wälchli
Chief Commercial Officer
ANYbotics
Outokumpu chose the ANYmal model from ANYbotics in these three pilot projects.
Why this four-legged robot?
Thorsten Piniek: It is important for us to have a rugged robot, following the IP67 standard. This is because we work with various chemicals, such as in the pickling process, and metals are melted in our plants in Finland and Sweden. Therefore, we are exposed to high temperatures, dust, and combustion processes.
What advantages and disadvantages do the ANYmal robots have over the model Spot from Boston Dynamics for Outokumpu?
Enzo Wälchli: At ANYbotics, we have a clear focus on industrial applications. This includes the IP67 protection class mentioned earlier, as well as the reliability and robustness required for operation in factories. As a result, the robot may be slightly heavier and may not move as elegantly, which can be important for the entertainment industry, but not for industrial use.
Another difference is that we have developed a system that is designed from end to end. We either install all the necessary sensors or work closely with partners to ensure full integration. As a result, the customer receives a tested and certified device that does not require any further modifications.
Another significant difference is that our four-legged inspection robot was developed for fully autonomous work right from the beginning. While it is possible to limit this autonomy and allow for more interaction, the robot operates independently based on its core concept. Scaling back this autonomy is much simpler compared to empowering a robot designed for interaction to achieve complete autonomy.
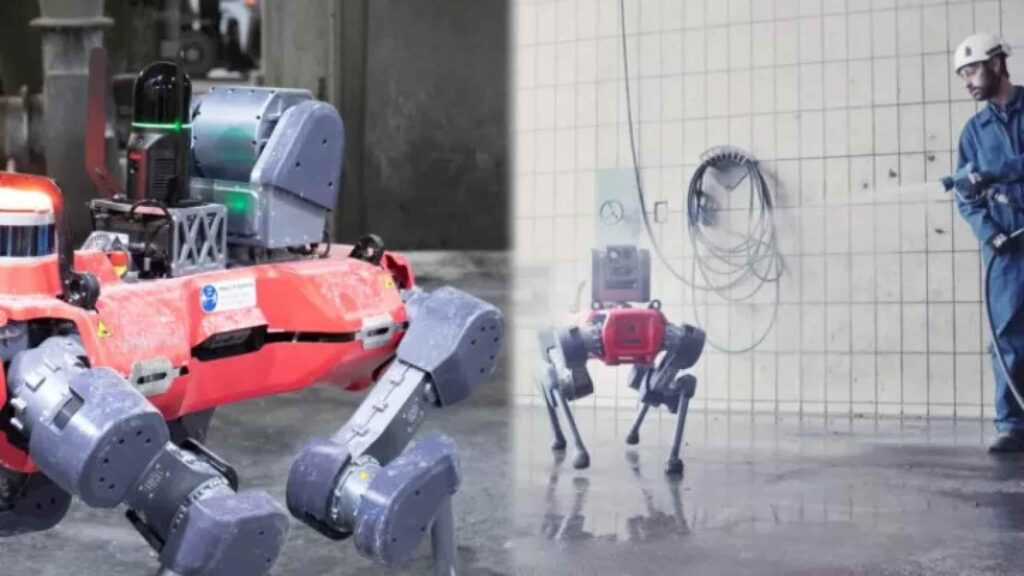
According to IP67, the robot is protected against dust and temporary immersion.
What does the automated inspection solution that Outokumpu now uses in Krefeld cost?
Piniek: We do not want to provide detailed comments on the prices. However, I can say that we are already making efforts towards implementation. My colleague Sebastian Kegel from the Krefeld plant is currently dedicating almost 100 percent of his time to learning about this four-legged robot. We will also ensure knowledge transfer between the different locations.
For example, a colleague from ANYbotics recently visited Krefeld to discuss various topics. One of the main focuses was on improving the reliability of the robot’s tours, which we refer to as missions. Additionally, we discussed enhancing the depth of inspection by defining checkpoints more precisely. As a user, it is important for you to develop new skills in these areas. These discussions primarily pertain to Sebastian’s area of responsibility, specifically occupational safety.
Sebastian Kegel:: Yes, this type of robot application was a new field for me. I am actually a mechanical engineering technician and have been with the company for 20 years. I worked in occupational safety for around a year before becoming a technical expert in the department where the robot is used. My colleagues and I are gradually working on this. We encounter new questions along the way, so it is beneficial that ANYbotics is always available. It all begins with the first training session, where you only scratch the surface. Meanwhile, I would dare to operate robots on my own, at least to some extent.
Piniek: During the familiarization phase, it is beneficial to have someone like Sebastian Kegel, who is familiar with the work and processes within the company. This is because the robots are trained in the specific environment they will be working in. The training process began almost two months ago, so we are still in the early stages. For instance, the robot is learning to navigate a specific staircase, figure out the best path, and avoid obstacles. This training process is similar to how one would train a dog.
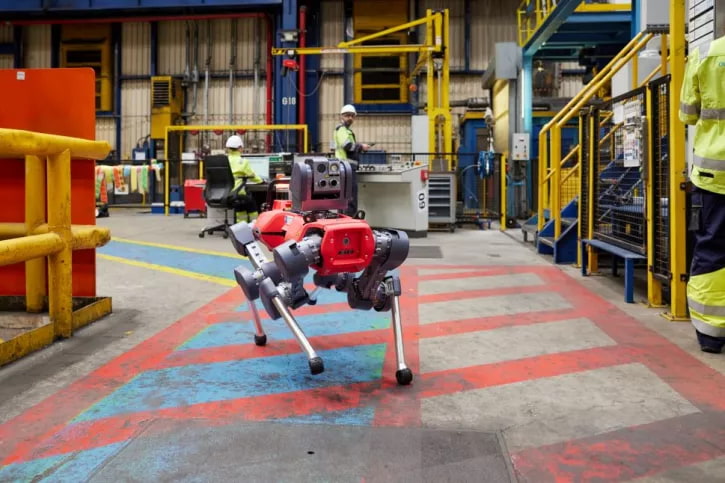
When the training is complete, the robot does its inspection missions autonomously and collects data.
(Courtesy: Outokumpu)
How do you engage with the robot when it meets you in the factory?
Kegel: As an uninvolved person, you don’t actually engage – the robot always stops first. There are various interfaces available for the operator, including remote access and online tools. When teaching the robot new tasks or missions, we use a laptop or tablet in a traditional manner, assuming it is compatible with the plant’s system.
What’s interesting is that ANYmal is just a component of the entire system. There is a comprehensive software package behind it. The data collected by the robot is saved, evaluated, archived, and compared. The robot is simply the visible part of the system – a mobile measuring point that moves within the factory.
What is the goal of Outokumpu with the project?
Piniek: It’s about occupational safety. Our goal is to gradually eliminate accidents and reach zero incidents. We achieve this by prioritizing the safety of our employees. Firstly, we aim to eliminate any potential dangers they may be exposed to. Secondly, we ensure the reliable operation of our systems.
The robot plays a crucial role in both areas. For instance, in our hazardous areas in Krefeld where we use hydrofluoric acid and nitric acid, the robot takes over tasks that would otherwise require human presence. It inspects the basement and performs necessary inspections. We can also assign the robot various measuring points to closely monitor the condition of the system and proactively address any issues. By doing so, we can plan repairs more effectively rather than relying on ad hoc measures.
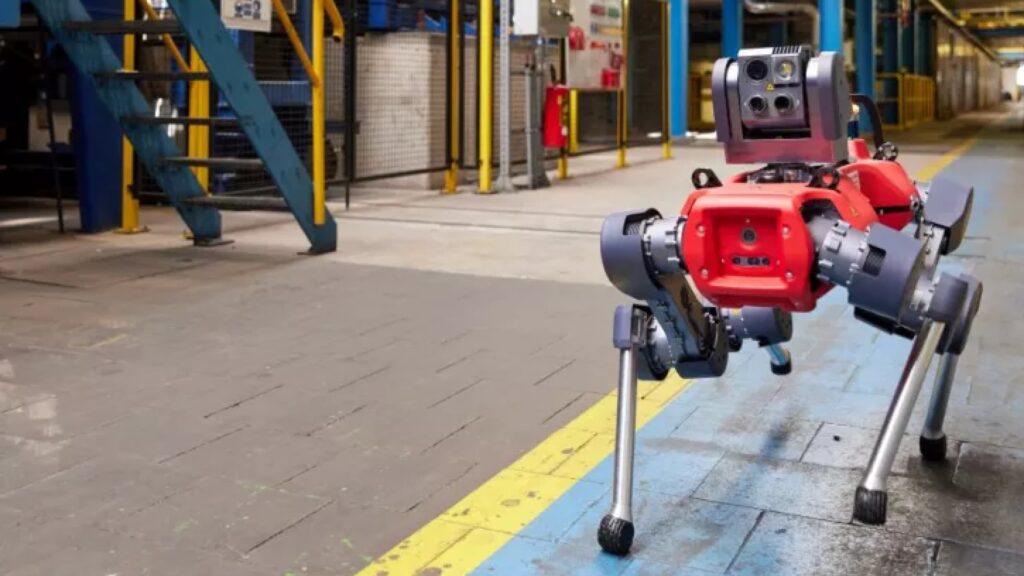
ROSIE logs into the WiFi to transfer data. The four-legged robot can also work offline.
(Courtesy: Outokumpu)
What sensors does the robot have to control the systems?
Kegel: We have the opportunity to capture classic pictures using the robot’s high-resolution camera. Another option is using a thermal image, where desired temperature ranges can be specified. If there is a deviation, the robot can generate different commands, such as taking additional pictures. The third option is frequency or noise detection. The robot can identify and compare different noises. For instance, a change in motor noise could indicate a problem. In such cases, we would plan for maintenance or replacement in the near future. The analysis of the data begins in the robot. The final analysis is then performed by the software or systems connected behind it. You evaluate the data again and compare current and previous data records.
Can you give an example from the past two months?
Kegel: Yes, we have already achieved some initial successes in test operations. However, we have not received any repair reports because the robot is not yet integrated in our systems. Nevertheless, I have noticed temperature deviations along our usual routes and have proactively reported these for maintenance. This allows us to address any issues earlier than we would have otherwise. In the future, these maintenance and repair reports will be generated automatically. Although we have not reached that point yet, it is one of the next steps we will take. Currently, we are in the process of building up the data records that the robot can use to compare current values. This training process takes some time, which is one of the reasons for the delay.
Wälchli: This process requires a lot of intelligence to be successful. Otherwise, the robot will return with ten blurry photos, resulting in a failed mission. To enable trend analysis, it is necessary to connect the interface to the end customer system. Companies typically have advanced predictive maintenance models for critical technology. Various processes are established to trigger an alarm, for example, when there are long-term changes in temperature or noise levels of a device. At this stage, human involvement becomes necessary as their experience is needed to interpret the significance of such changes.
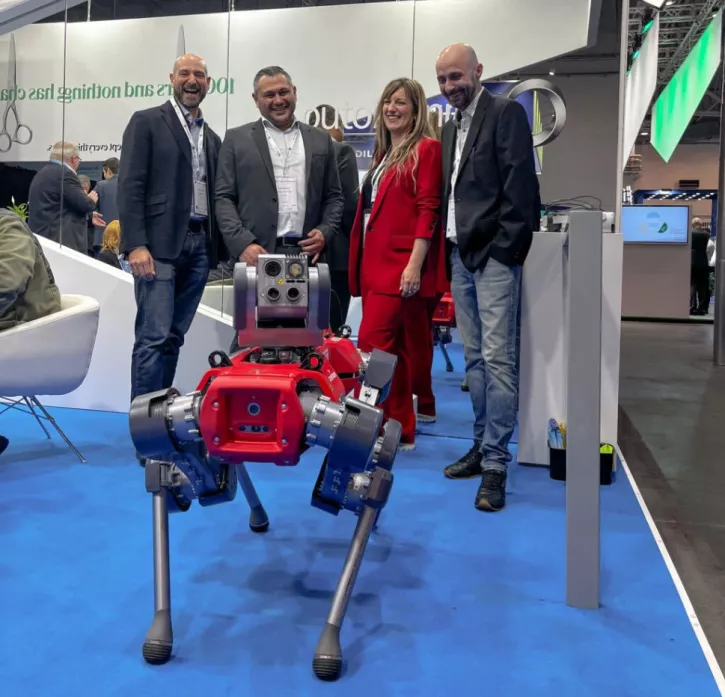
Outokumpu and ANYbotics announced the pilot project at the Green Steel conference in April 2023. The steel manufacturer uses a robotics-as-a-service offer from the manufacturer.
(Courtesy: Outokumpu)
How has the training process been going so far?
Kegel: The first step is for the robot to move safely within our factory and know its intended destinations. For example, it should be able to receive an order to go to a specific system and navigate through one of several inspection routes to get there. It should be able to do this autonomously, and we are currently working on achieving that capability. Initially, the robot will use the same routes as our employees for its inspections, unless it needs to access special areas. The second step involves collecting data and transferring it to the interface via a server, and then defining the relevant processes.
How long will it take for the four-legged robot to move safely in the facility and provide data as you have just described?
Kegel: In my opinion, this question is difficult to answer. Therefore, I believe we will need an additional month or two before the entire system runs smoothly. I also depend on my colleagues from IT and ANYbotics.
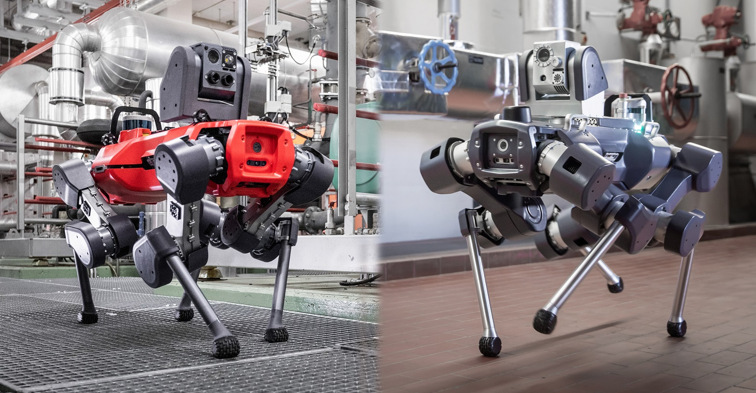
How does ANYmal know where it is – with GPS?
Wälchli:: No, GPS would be too imprecise. ANYmal has a lidar sensor that uses a laser to measure the distance to existing objects and obstacles. In the first step, you map the entire system. This data appears as point clouds. In the second step, using the saved map, the robot compares its current position during subsequent missions and determines its location. This method is called SLAM in technology jargon: Simultaneous Localization and Mapping. The robot moves and updates its map simultaneously. ANYmal also understands where it can go and what movement options it has.
Doesn’t it bother it that this environment is constantly changing, for example, because people pass by?
Wälchli:: No, ANYmal can handle it.
Have there been any concerns among the workforce that the robot could cost jobs?
Wälchli:: Companies can use such robots to automate tasks that people do not want or should not do, such as working in hazardous areas. Additionally, if one wants to increase the productivity of systems, a significant amount of data is required, which is currently lacking. Robots generate this data, making work safer and more productive.
Piniek:: We involved our workforce at an early stage when the decision was made to bring this robot to our factory. We even held a competition where the workforce could suggest and choose names for the robot. The response was overwhelmingly positive. I would say that there is now widespread acceptance.
And what name did he get?
Piniek:: It was decided that the robot would be called ROSIE: Robotic Operating System for Industrial Engineering. I recently had the opportunity to see it in action for the first time in person. Of course, it is a new and different experience when a robot moves around the factory. However, one quickly becomes accustomed to it.
How is it going now?
Piniek: In Krefeld, we are currently working on missions in the factory and the first inspection points. The second robot for the acid sector arrived at our plant in Sweden in September. Additionally, we are taking another step towards the end of the year: our plant in Tornio will receive its robot. Tornio is a city located in the north of Finland, on the Finnish-Swedish border. The robot will be exposed to very low temperatures there. Based on these three pilot projects, we will work with ANYbotics to determine the final implementation plan.